Notes on Value-Stream Mapping
A value stream is the sequence of activities required to design, produce, and deliver a good or service to a customer. – Value Stream Mapping by Karen Martin and Mike Osterling
Value-stream mapping is a technique for identifying bottlenecks and improving flow using lean methods. Flow is the movement of work through a production system. Improving flow implies reducing the time works spends in queues, bring reworked or other forms of wastes.
John Shook and Mike Rother in Learning to See state that most improvement efforts fail because they don’t see the whole. The result is that one part of the system improves only for wastes and bottlenecks to emerge in other parts of the system. Value-stream mapping helps us take a holistic view of the system before we jump in to make improvements.
To see the whole, value-stream mapping requires whole-team participation i.e. everyone involved in production processes gather together in one room to create the map.
Value-stream mapping comprises the following high-level activities.
- Pick a value-stream
- Map the current state
- Map the future (desired) state
- Set goals and execute improvements
- Repeat steps 2 through 5
Note that a separate value stream should be drawn for each product-family (a set of products that have a high number of common processing steps). It is prudent not to get too bogged down in picking which value-stream to map. More often than not, the improvements that come out of one value-stream map will help improve other product families too.
Below we’ll focus our attention on creating the current state map.
Creating the current state map
The sequence below is not definitive – it is just a workflow I have in mind as I prepare to do mapping activity.
- List out all the activities (processes) and arrange them as a timeline
- Add actors involved in each activity
- Add a symbol for inventory between processes (where it exists) along with the count of inventory
- Add information systems (e.g. Jira, Notion) that each process uses
- Add the following details to each process
- Process time (PT) a.k.a. “touch time”, the time that work is being worked upon
- Lead time (LT), time inclusive of waiting
- Percentage complete & accurate (%C&A), as reported by downstream process
- Any additional metrics suitable to the value-stream
- The barriers to flow (described below)
“Flow” is the movement of work from one process to the next without interruption or delay. Barriers to flow include:
- Non-value adding work
- Back-flow due to defects
- Waiting
- Creation of inventory
- Hand-offs
- Inspection
- Work that could be standardised or automated
A more detailed list by Karen Martin and Mike Osterling is shared towards the end of the article.
A handout PDF that I used for a mapping activity can be found here.
Summarising the metrics
Once the metrics of each activity are listed, they can be summarized into a table consisting of:
- Total process time (PT)
- Total lead time (LT)
- Activity ratio (PT/LT)
- Rolled %C&A (%C&A of each step multiplied together)
Notation
This is an adapted notation that I used on an online white-boarding tool.
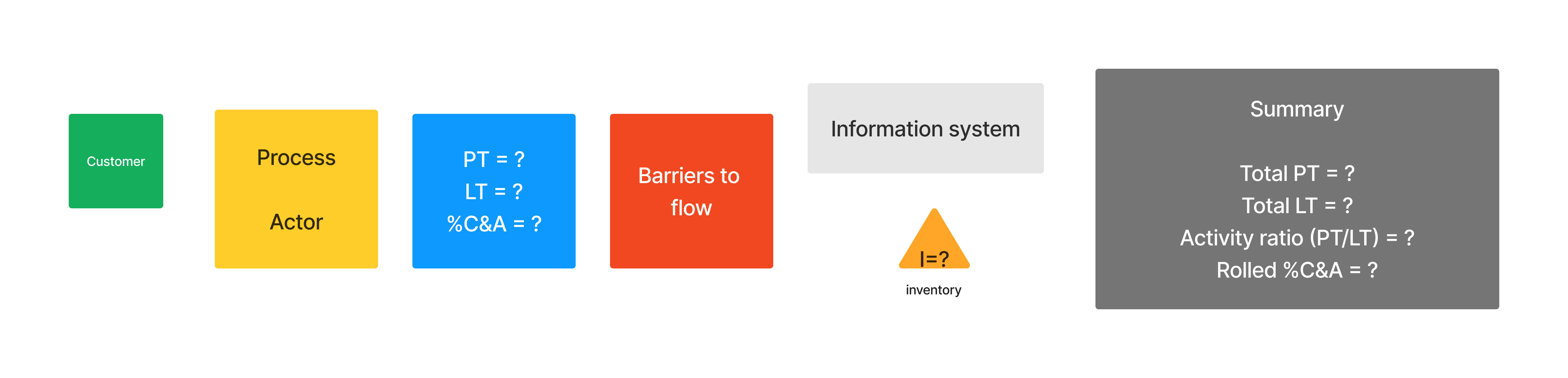
Sample map
A sample diagram I drew with a client with details blurred out.
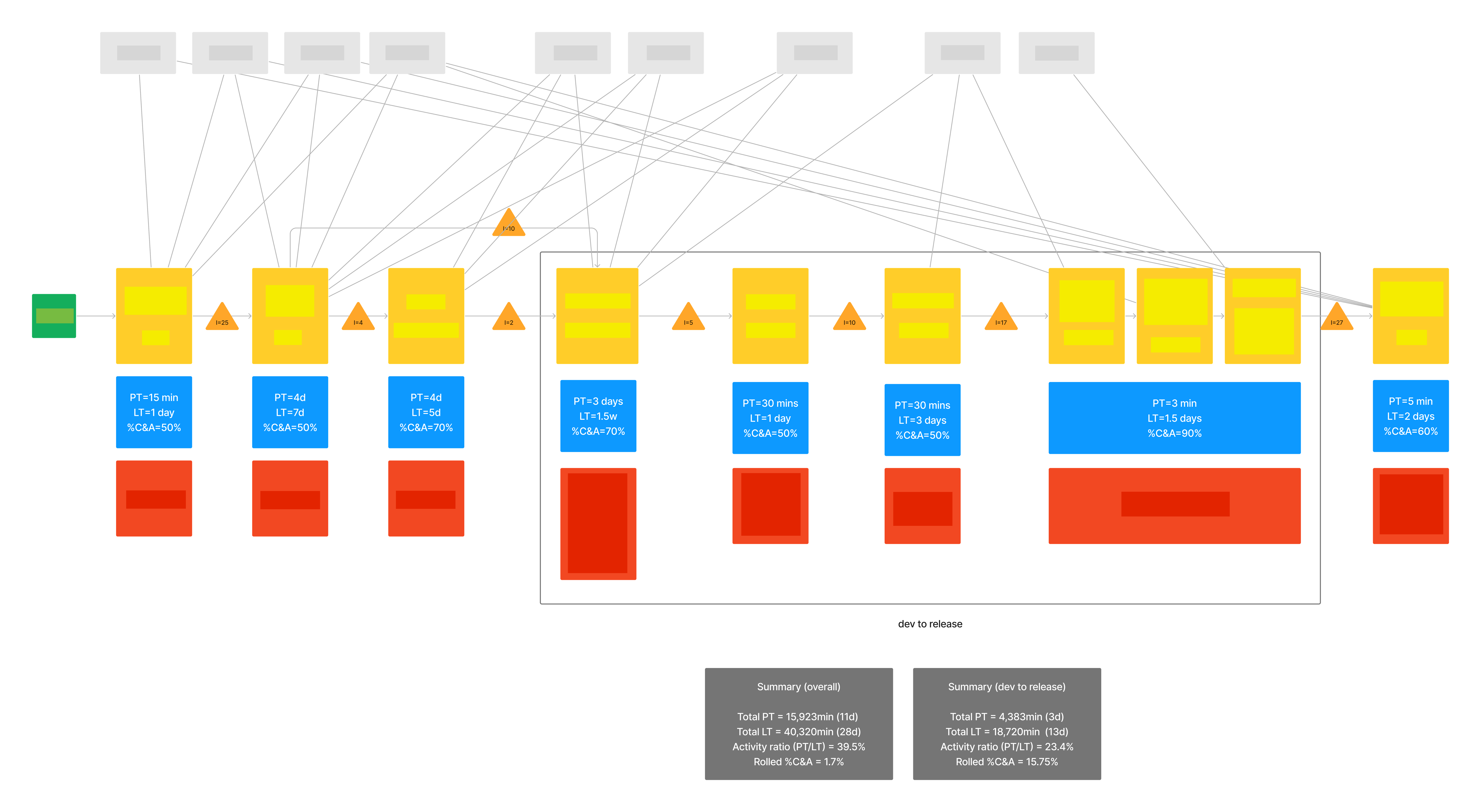
Barriers to flow
Karen Martin and Mike Osterling describe a set of common problems that current state mapping may reveal. They are listed below for reference.
- Loop-backs
- Unnecessary hand-offs
- Rework due to errors and lack of clarity
- Batching
- Functions missing or getting involved too early or too late in the process
- Redundant activities
- High variation in how work is performed
- No documented standard work
- Excessive inspection (review, approval, audits)
- Overspecialization of staff
- Existing technology is not fully leveraged
- Under-utilization of skills
- Compliance overkill
- Delays due to juggling multiple responsibilities
- Push and overburden
Relevant
A worked example of Value-Stream Mapping
Value-stream maps can be daunting at first glance like these maps on Google Images. ValueTech (a made-up software company for the purpose of our example) thought so too until they...
Leveraging 1x1 production to improve flow
In its ideal, 1x1 production means that parts move from one value-adding processing step directly to the next value-adding processing step, and then to the customer, without any waiting time...
Automobile assembly line kata
This is the blueprint for practical workshop to learn about lean principles. We run a simulation of an automobile assembly line using LEGO blocks. If LEGO blocks are not available,...
Just because inventory is invisible...
Inventory is unfinished work – that which hasn’t yet reached the customer. The presence of inventory indicates that costs have been incurred however value or revenue hasn’t been extracted. And...
Recent posts
Test pyramid and ice-cream cone
The test ice-cream cone is a strategic anti-pattern. It indicates excessive reliance on expensive and flaky forms of testing, such as manual and end-to-end, especially for components that could otherwise...
First experience with Event Storming
Event Storming is a technique that uses post-it notes to map out a business domain. Alberto Brandolini initially used it as a means to identify aggregates in the context of...
My library
This is a list of books I have read in the first decade of my professional career. I started quite late so most if not all were read in the...